Natural gas, a hydrocarbon gas comprised predominantly of methane, is an important global energy source. For decades, countries have made it part of their energy policy to switch from coal to cleaner burning natural gas, increasing its demand. Transporting gas by any means other than high pressure pipe is challenging and often infeasible. To make natural gas more easily transportable portable, it’s chilled to -260◦F (-160◦C) where it liquifies and its volume shrinks 600 times. Once liquified, LNG can be efficiently transported mostly anywhere in the world aboard, LNG carrier ships or distributed locally on LNG tank trucks or train cars.
LNG Export Liquefaction Plants
LNG Export Liquefaction Plants are massive facilities that can liquify millions of tons per year of LNG (Liquefied Natural Gas), LPG (Liquid Propane Gas), and other gases. Liquefaction plants are frequently located near major coastal waterways so the LNG can be loaded aboard LNG carrier ships for export to locations around the globe. That often means they are also located near business or residential communities. Natural Gas, if released, is not only flammable, but can also cause negative health effects or asphyxiation to people nearby. As a result, LNG Liquefaction planners must navigate a lengthy and expensive health and environmental regulatory approval process, potentially limiting the size and location of the planned facility.
Peak Shaving LNG Plants
Unlike Export LNG Liquefaction plants, Peak Shaving LNG plants are much smaller and serve only their local community. LNG is liquefied or brought in by truck when natural gas prices are low and stored in large tanks. Later, in winter or summer when energy is at peak demand, the LNG is re-gasified (converted back to a gas) and used at nearby power plants to generate electricity. Even though much smaller, Peak Shaving LNG plants still pose a significant risk to the health of the residential and business communities nearby and must go through a similar health and environmental regulatory approval process. For both plant types, obtaining regulatory permitting is no easy task. Planners must simulate a major release of natural gas from a full pipe rupture and schedule a walkthrough of the area to ensure the plant is not at significant risk. This means a large safety envelope around the plant is necessary putting limitations on where the plant can be constructed as well as the full capacity of LNG that can be produced.
Solution: Dual Containment Vacuum Insulated Pipe (VIP)
The solution that has been deployed for decades is simple, put pipe inside pipe to reduce the risk of catastrophic release. Known as dual containment or secondary containment, the LNG carrier pipe is secured inside a larger pipe or jacket. In the unlikely event the carrier pipe fails at any point, the LNG would be contained safely within the outer jacket. Instead of having to model a full pipe containment failure, the designer models only a 2in diameter hole in the pipe with an assumed leak many times less than they would without dual containment.
The use of dual containment offers operators another major benefit. By pulling a high vacuum between the carrier pipe and jacket pipe, the system can utilize the super insulating properties of Vacuum Insulated Pipe (VIP). In VIP systems, a high vacuum is pulled between the inside pipe and the outer jacket pipe creating an annular space without the capacity to transfer heat via conduction or convection. The carrier pipe is then wrapped in special foil/paper, called Multi-Layer Insulation (MLI), to significantly reduce heat transfer through radiation. The resulting system has almost no heat transfer and can transport cryogenic liquids over long distances or keep them liquified for extended periods.
VIP is known to be a better insulator vs. mechanical insulation by up to 20 times and with a smaller footprint. VIP also doesn’t require the continuous inspection and maintenance necessary to maintain mechanical insulation. By using Vacuum Insulated Piping on the cryogenic liquids, designers can expect favorable regulatory approvals while providing continuous savings to the operator. For all parties involved, it’s a win-win.
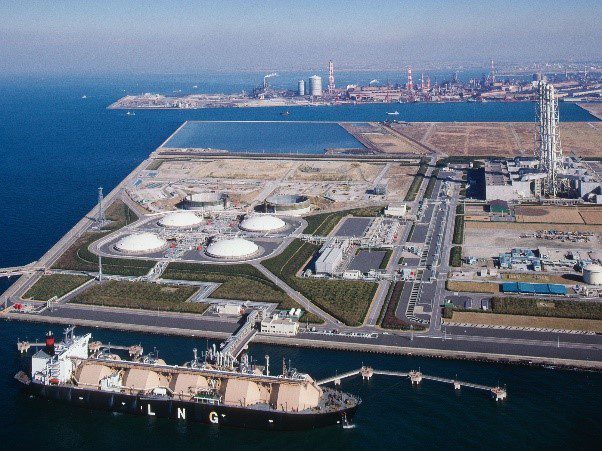
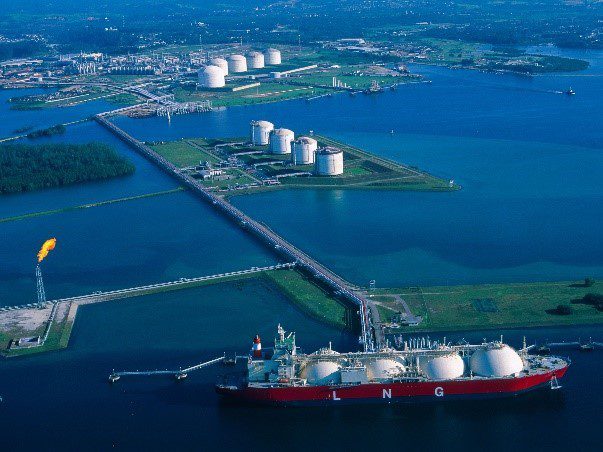
CryoWorks Has A Solution for You
When it comes to Vacuum Insulated, Dual Containment Pipe, CryoWorks has a solution that is right for you. Our VIP is the preferred method for transferring cryogenic liquids and is unmatched in safety, reliability, and cost-effectiveness. CryoWorks provides best in industry delivery and service while being relentlessly dedicated to:
- Complex System Design & Engineering
- Expert Project Management
- Experienced Sales Staff with Component and System Expertise
- Easier & faster installation
- Shop fabricated and tested to order
Our products are highly engineered and rigorously proven:
- +20 years life expectancy
- Low to no maintenance costs for the life of the system
- Reduction of Boil-Off Gas (BOG) and lost commodity cost
- Longer piping runs with fewer expansion loops
- Smaller diameter compared to conventional insulation, taking up less pipe rack space
- Built to ASME B31.3, B31.12, and NFPA 59A
We offer many insulated piping solutions including:
- Rigid engineered pipe with internal or external expansion joints
- Pre-Engineered rigid pipe
- Jacketed flexible hoses
- Full containment piping